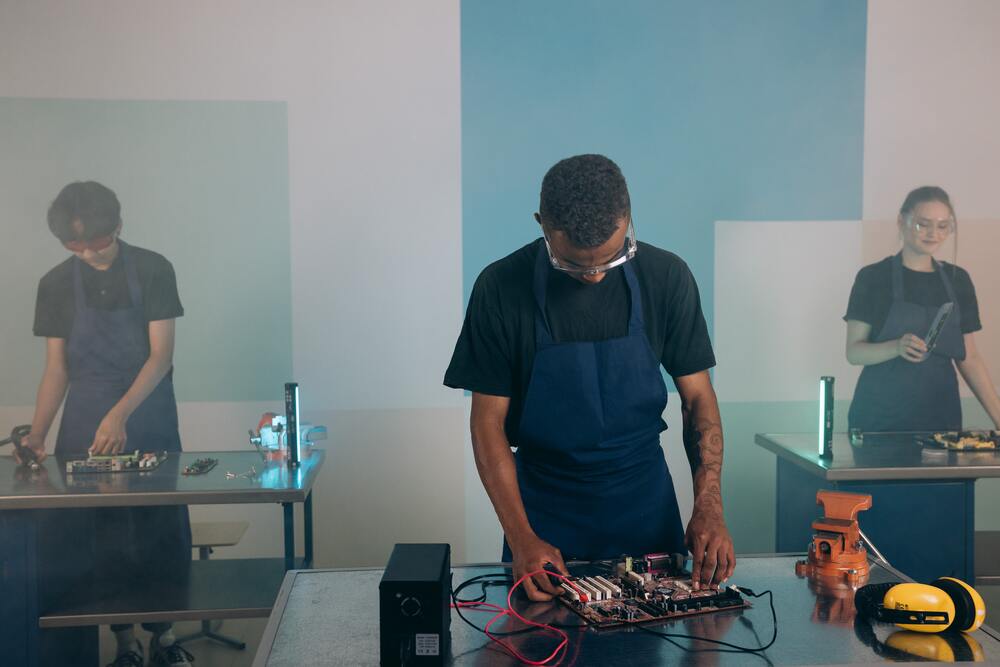
Dalam industri manufaktur, kualitas produk dan efisiensi
produksi sangatlah penting. Salah satu metode yang digunakan untuk mencapai
tujuan tersebut adalah Pokayoke, sebuah konsep yang bertujuan untuk mencegah
terjadinya kesalahan atau cacat dalam proses produksi. Dalam artikel ini, kita
akan membahas tentang penggunaan sensor cahaya sebagai salah satu metode
Pokayoke yang efektif di industri manufaktur.
Apa itu Pokayoke?
Pokayoke, yang berasal dari bahasa Jepang yang berarti
"mencegah kesalahan," adalah sebuah pendekatan yang digunakan untuk
mengidentifikasi dan mengurangi risiko terjadinya kesalahan manusia dalam
proses produksi. Tujuan utama dari Pokayoke adalah mencegah terjadinya cacat
atau kegagalan produk sejak awal proses produksi, bukan hanya mendeteksi
kesalahan setelah proses selesai.
Sensor Cahaya dalam Manufaktur
Salah satu jenis sensor yang sering digunakan dalam
implementasi Pokayoke adalah sensor cahaya. Sensor cahaya dapat digunakan untuk
mendeteksi perubahan intensitas cahaya atau variasi warna yang terjadi selama
proses produksi. Dengan memanfaatkan sensor cahaya, produsen dapat memastikan
bahwa setiap langkah produksi dilakukan dengan benar, serta mengidentifikasi
dan mengatasi masalah potensial sebelum terjadi.
Penerapan Pokayoke dengan Sensor Cahaya
- Verifikasi
komponen: Sensor cahaya dapat digunakan untuk memverifikasi keberadaan
dan kecocokan komponen selama proses perakitan. Dengan menggunakan pola
intensitas cahaya yang telah ditentukan sebelumnya, sensor cahaya dapat
mengidentifikasi apakah komponen yang diperlukan sudah ada atau tidak.
Jika komponen tidak terdeteksi, sistem dapat memberikan peringatan atau
menghentikan proses perakitan.
- Pendeteksian
kesalahan dalam pengepakan: Dalam proses pengepakan, sensor cahaya
dapat digunakan untuk mendeteksi keberadaan atau ketiadaan produk di dalam
kemasan. Jika sensor cahaya tidak mendeteksi adanya produk yang seharusnya
ada, maka sistem dapat memberikan peringatan kepada operator atau bahkan
menghentikan mesin pengepakan untuk mencegah pengiriman produk yang tidak
lengkap.
- Pemantauan
kualitas: Sensor cahaya juga dapat digunakan untuk memantau kualitas
produk secara real-time. Misalnya, pada proses pengelasan, sensor cahaya
dapat mengidentifikasi adanya cacat pada sambungan las dengan mendeteksi perubahan
pola cahaya yang tidak diinginkan. Hal ini memungkinkan operator untuk
melakukan tindakan perbaikan atau penyesuaian segera sebelum produk
mencapai tahap berikutnya.
Keuntungan Penggunaan Pokayoke dengan Sensor Cahaya
- Meningkatkan
efisiensi: Dengan mencegah terjadinya kesalahan sejak awal proses
produksi, waktu dan biaya yang sebelumnya digunakan untuk mengatasi
kesalahan dapat dihemat. Dengan menggunakan sensor cahaya dalam penerapan
Pokayoke, produsen dapat meningkatkan efisiensi produksi dengan mengurangi
waktu yang terbuang untuk mengidentifikasi dan memperbaiki kesalahan.
- Meningkatkan
kualitas produk: Sensor cahaya membantu memastikan bahwa setiap
langkah produksi dilakukan dengan benar dan sesuai standar kualitas yang
ditetapkan. Dengan mendeteksi potensi cacat atau kesalahan pada tahap
awal, produsen dapat mengambil tindakan perbaikan yang cepat untuk
menghindari produksi produk cacat. Hal ini berdampak pada peningkatan
kualitas produk akhir dan kepuasan pelanggan.
- Mengurangi
biaya perawatan: Dengan menggunakan sensor cahaya untuk mencegah
kesalahan dalam proses produksi, produsen dapat mengurangi biaya perawatan
dan perbaikan. Dengan mengidentifikasi masalah secara dini, mereka dapat
mengambil tindakan yang tepat sebelum kerusakan yang lebih serius terjadi.
Hal ini mengurangi kebutuhan akan perbaikan besar-besaran dan downtime
produksi yang mahal.
- Meningkatkan
keamanan kerja: Implementasi Pokayoke dengan sensor cahaya dapat
membantu meningkatkan keamanan kerja di lingkungan manufaktur. Dengan
mendeteksi kesalahan atau ketidaktepatan, sensor cahaya dapat
memperingatkan operator tentang situasi berpotensi berbahaya atau
berpotensi menyebabkan cedera. Hal ini membantu mengurangi risiko
kecelakaan kerja dan menciptakan lingkungan kerja yang lebih aman bagi
para pekerja.
- Meningkatkan
produktivitas: Dengan mengurangi kesalahan dan cacat dalam proses
produksi, produsen dapat meningkatkan produktivitas secara keseluruhan.
Kurangnya kesalahan berarti lebih sedikit waktu yang terbuang untuk
memperbaiki masalah, yang pada akhirnya mengarah pada peningkatan output
produksi. Ini membantu produsen mencapai target produksi dengan lebih
efisien.